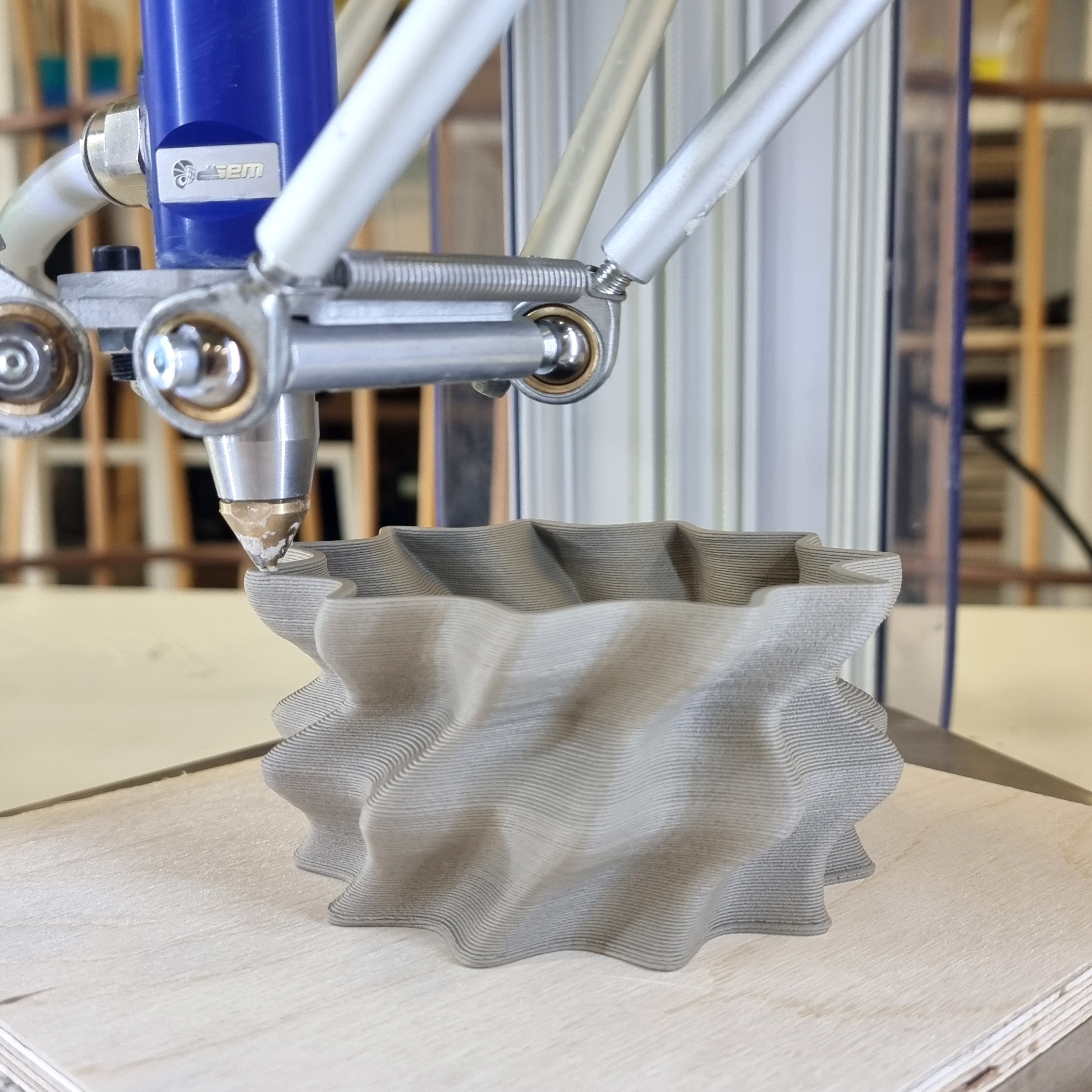
Get Geeky With Me: Parametric Design
At Duke Makes we are always trying to push the boundaries of our creative practice; every couple of months we like to pick a new research topic to get very geeky about. This allows us to explore areas that we wouldn't necessarily be able to do through commercial projects.
Our focus for the last couple of months has been parametric design. Broadly, this is a design process whereby design elements are produced by an algorithm written by the designer. This allows complex, customisable forms to be created that would be impossible to achieve manually.
The choice to explore this approach came when we were considering how to maximise the potential of our 3D printers.
Often 3D printers are used as a quicker substitute for traditional manufacturing methods - they are high precision and can produce forms impossible to make by hand.
It turns out the best way to make something that only a machine like the 3D printer could make is to ask another machine to design it.
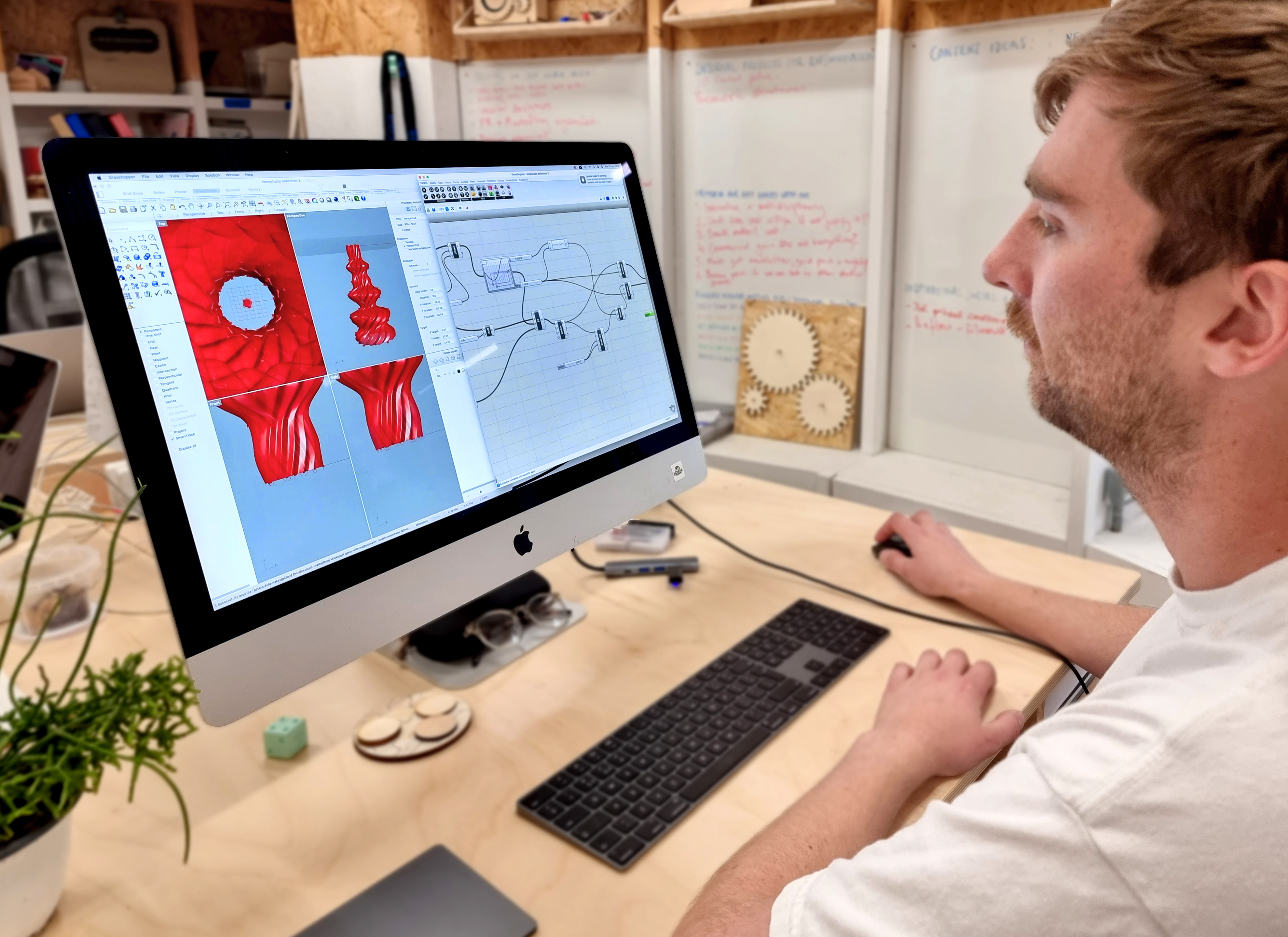
Duke Makes manager Liam spent a couple of evenings wrapping his head around the programming language required to create successful parametric designs. We’ve been using the program Rhino with a grasshopper programming plug-in; grasshopper is a visual programming language where data and functions are represented as a flow diagram, helping you to understand the points of function throughout the algorithm and how they link together.
In this program, different parameters can be fed into the algorithm in the form of anything from numbers to images. The model will then interpret this data and plot a series of points in 3D space that can be woven into surfaces and volumes. Because the input data can vary massively, it’s possible to create a huge range of forms within minutes.
Using this method, we created a range of forms and applied them to our FDM and Clay printer.
We believe there’s huge potential for this process, particularly in the world of interior design. It would be straight-forward for the designer to adjust the structure of the design and create specified, unique pieces to fit within their scheme. We used translucent recycled PET filament in our FDM printer to create a series of unique pendant lights.
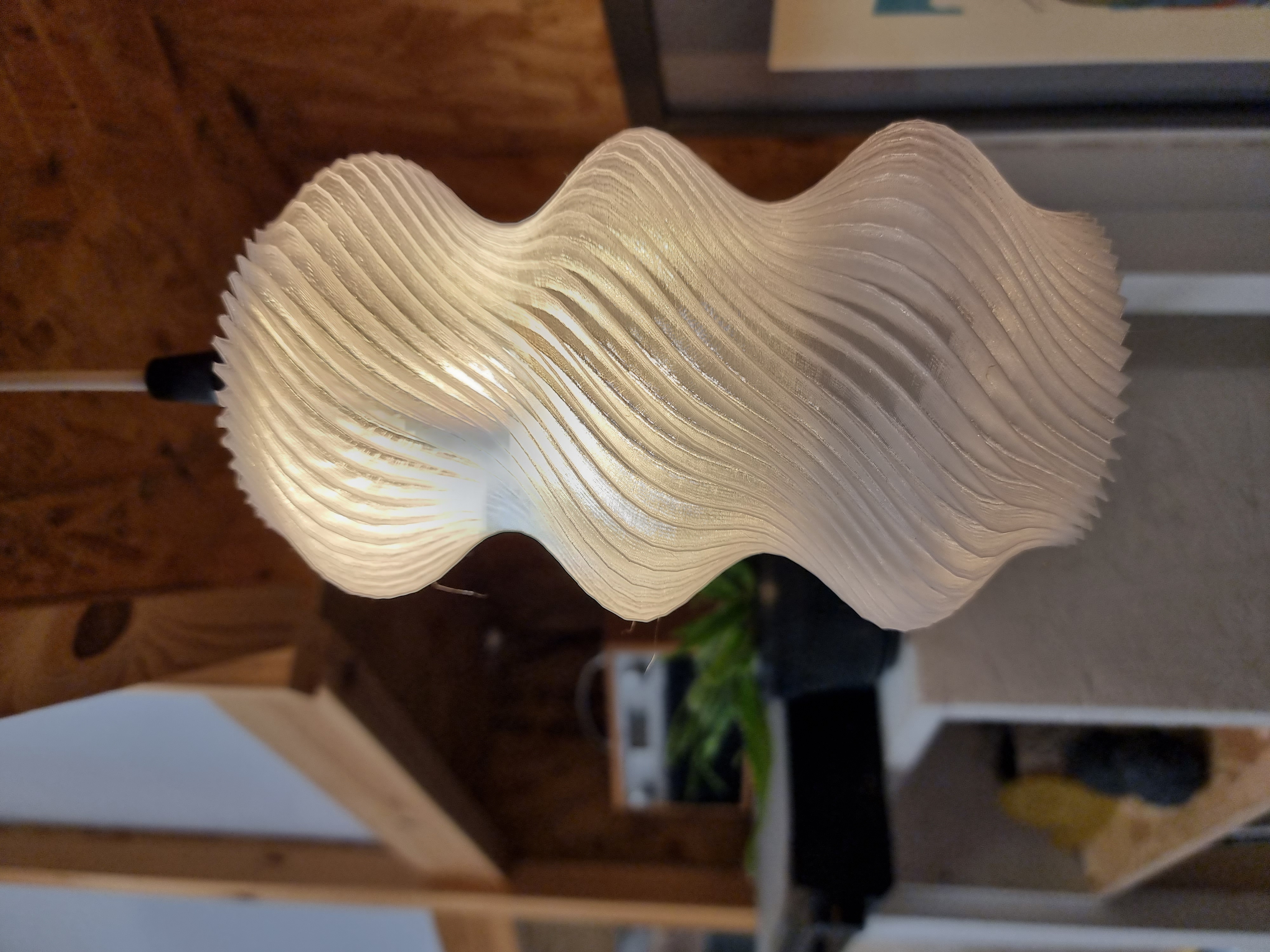
For the clay printer, we created 2D grayscale patterns and then designed an algorithm that would overlay this in 3D onto a cylinder. This resulted in a unique set of vases that would be impossible for a potter to create by hand. This process could easily be scaled up to create display pedestals or sculptural pieces.
Our learning curve was greatly helped by our collaboration with our neighbours, Sunken Studio, who helped us to refine our process. They advised us on everything from clay formulation to glazes to the ideal thicknesses to achieve a good firing.
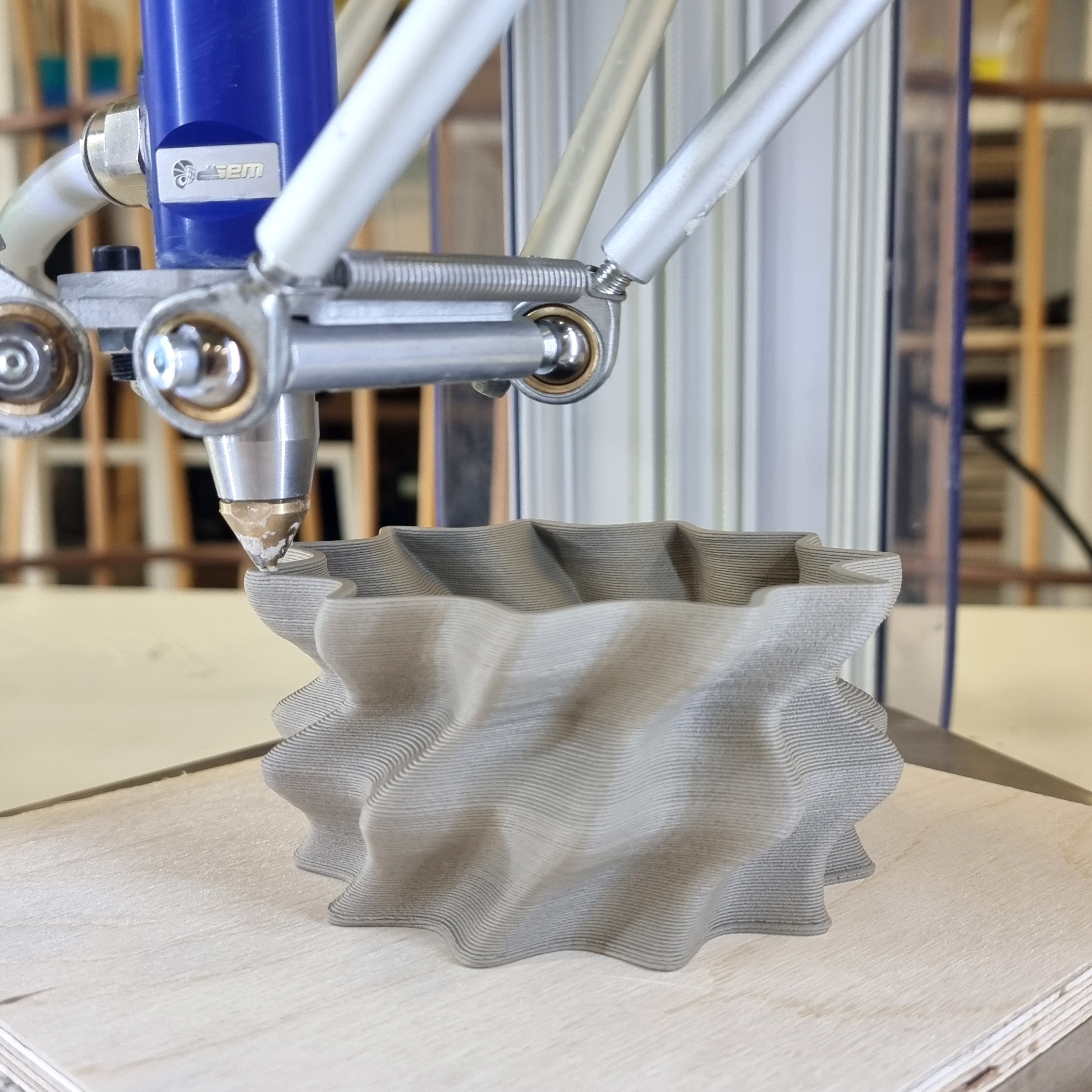
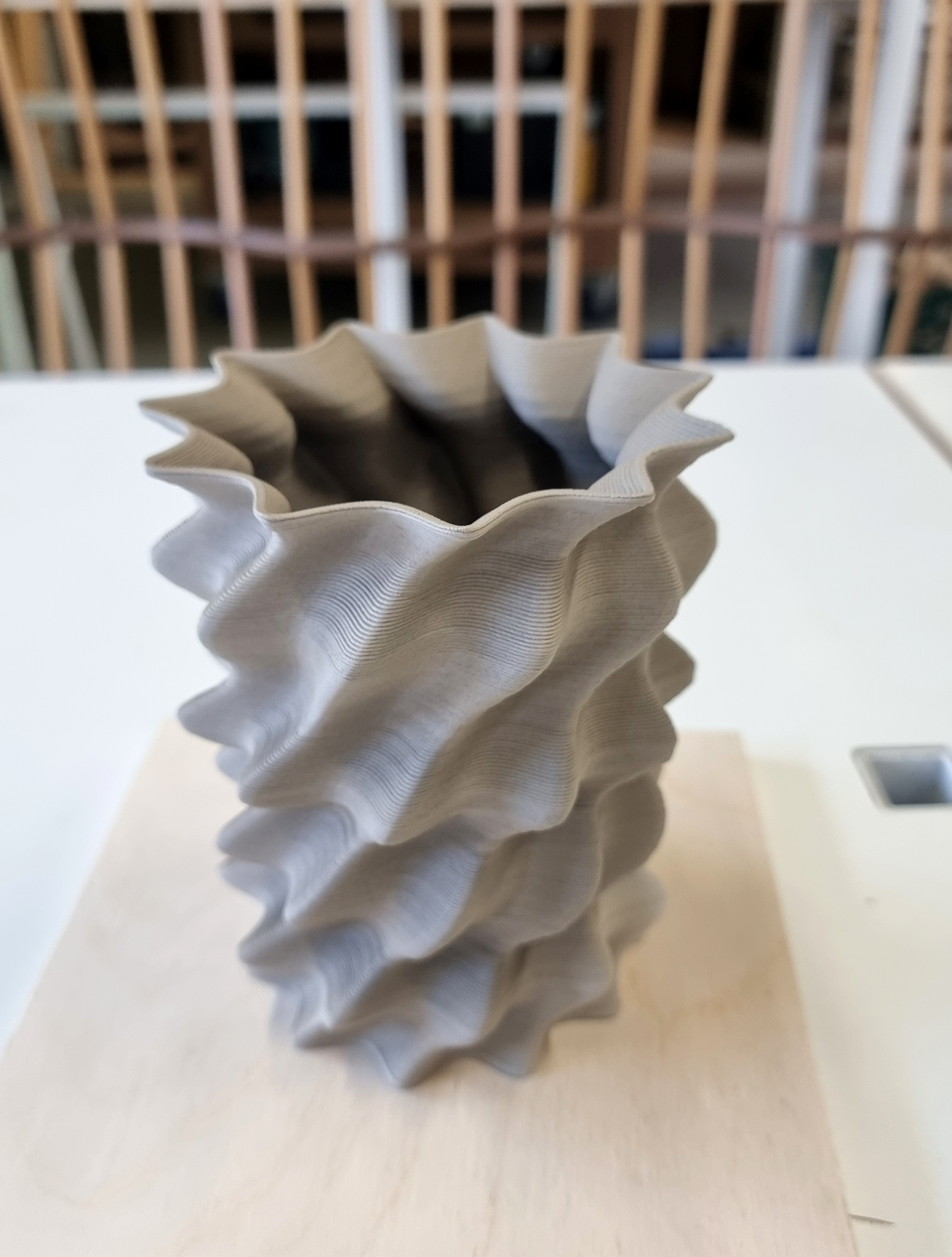
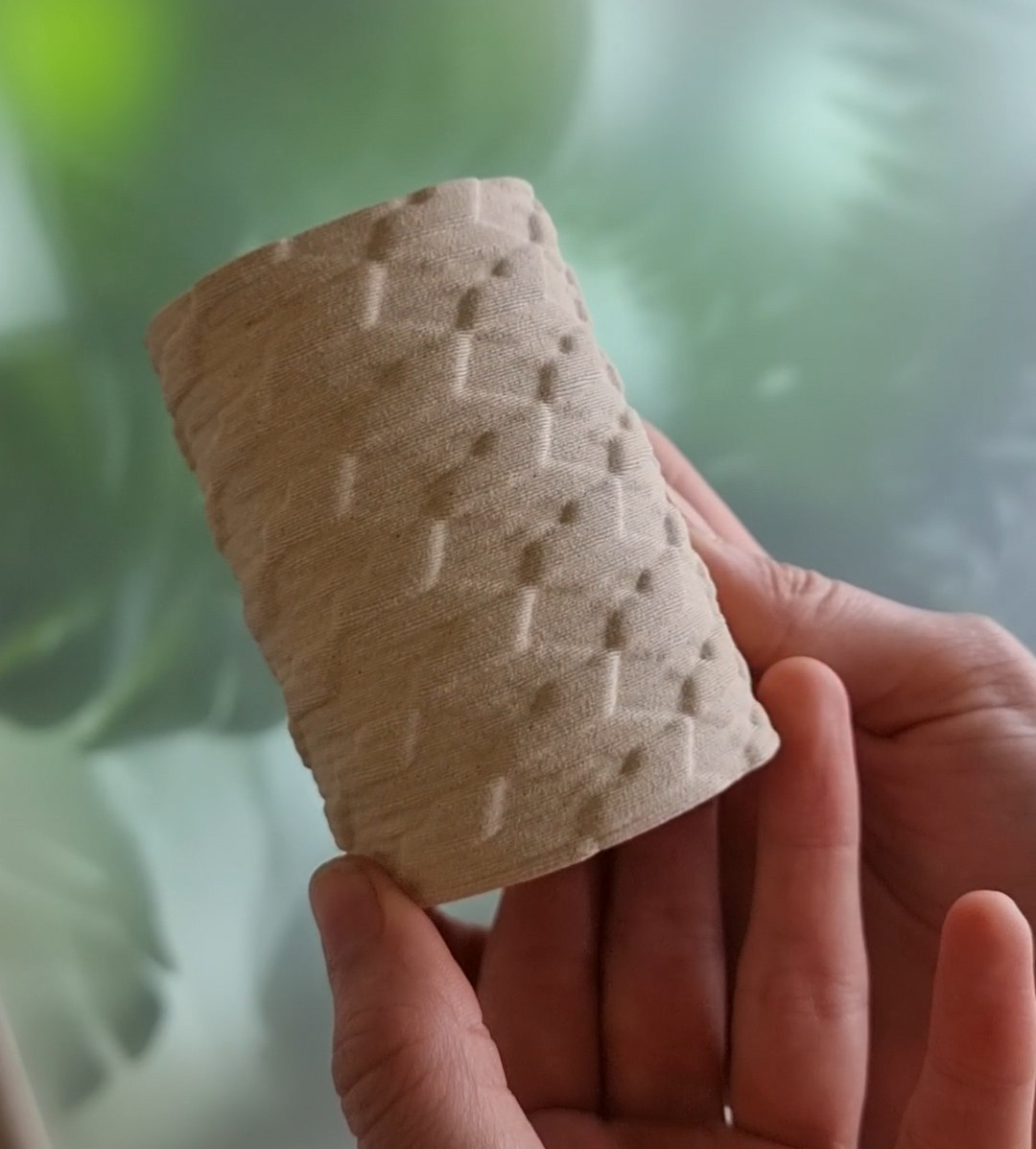
Of course, parametric design isn’t limited to 3D printing. Any process that uses a digital manufacturing method - where large numbers of similar but varying components can be manufactured (eg. CNC router, laser cutting) - can make use of this.
There are excellent examples of pavilions, facades and interiors being created using this method. Take this incredible pavilion designed as a festival dancefloor, designed by architecture studio, Hylemo.
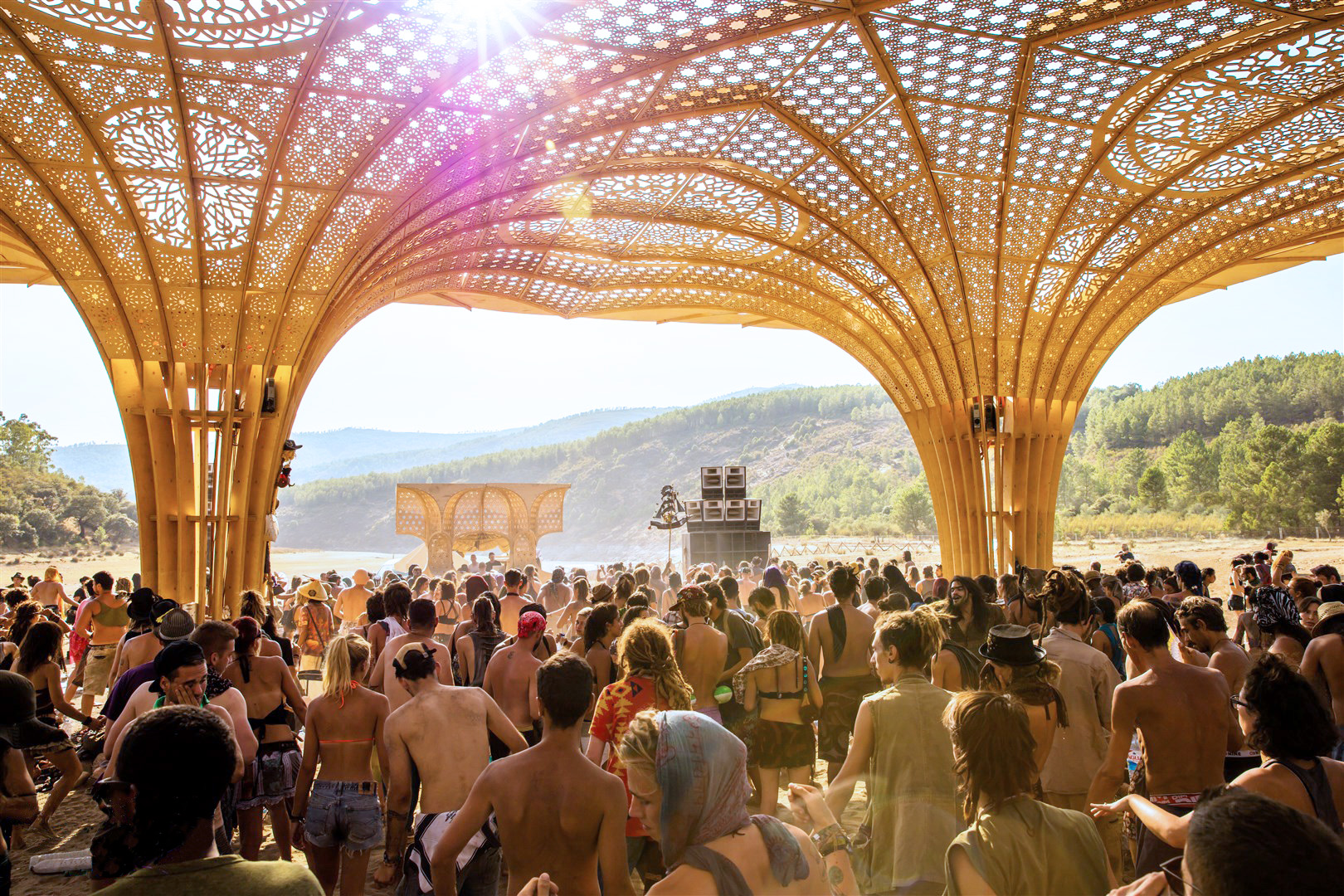
They explained to It’s Nice That, “As a studio we use algorithms to maximise inexpensive materials such as timber. The Lost Temple piece has been developed and designed using parametric software. Creating a parametric model is what allows us to produce a piece of this size entirely from CNC cut plywood.”
We would love the opportunity to create something large scale on our CNC router. If you can see this design approach influencing one of your projects, get in touch via our website.
What to read next
about it
Get the latest news
Sign up to our newsletter to be the first to hear about everything we’re up to, and get early access to events, workshops and more.