.png)
White Label Manufacturing
Ideas are found in strange places. On a commute, in our homes, or in a dusty record sleeve found at a carboot sale. One record becomes 5, which becomes 20, then suddenly your shelves are overflowing and - oh! A light switches on.
At Duke Makes, we know that every problem has a solution. That is why we were excited when Chris Cox, founder of Infinite Archive, came to us with an idea for an expandable vinyl storage solution. We had a chat with Chris about his experience with our Design & Create service at Duke Makes.
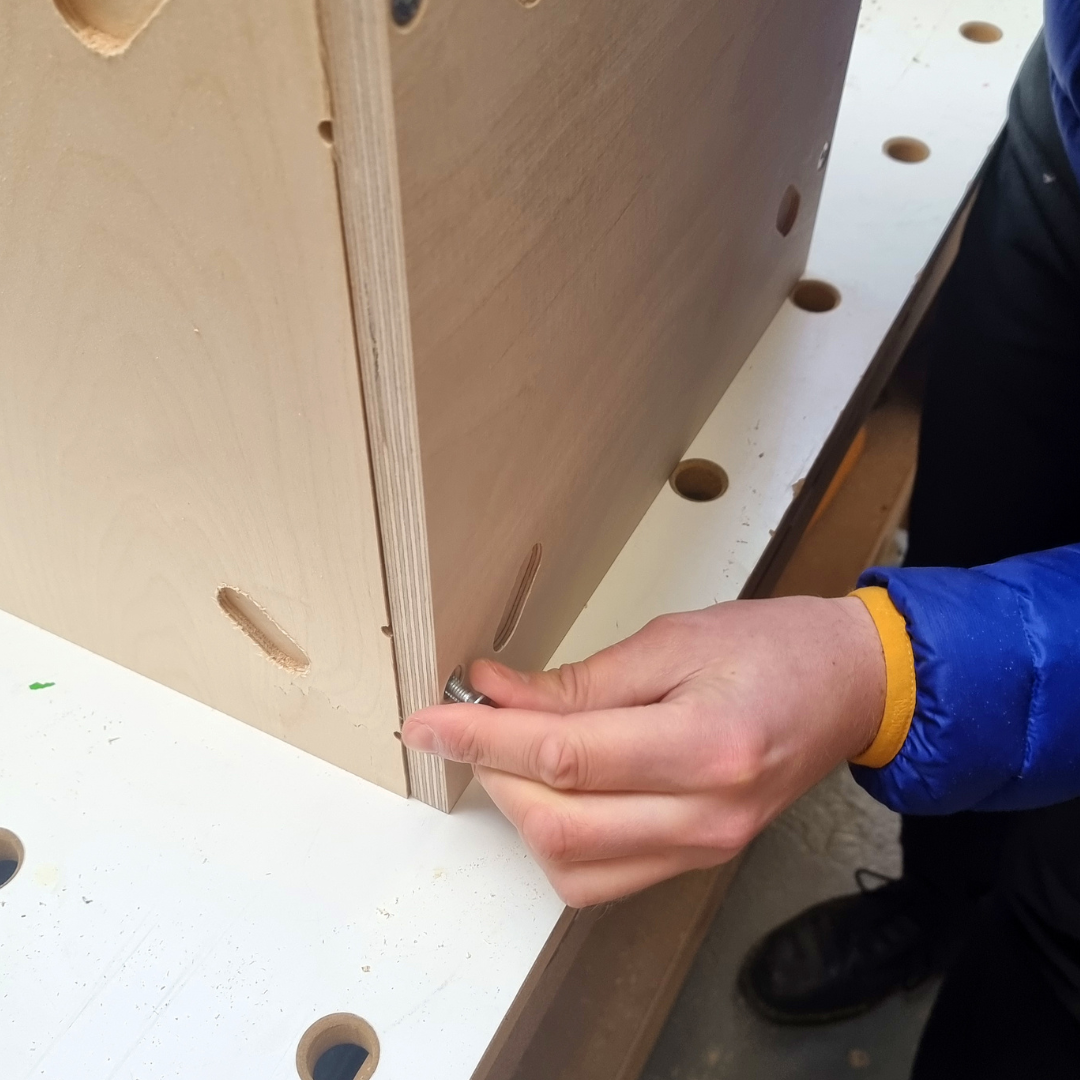
Where did it all start?
“The whole idea of doing it was really born out of me outgrowing my current vinyl storage at home. I’ve got two units stacks on top of each other. All my records were too tightly packed so what do I do? Do I get another shelf, where do I put it? I didn’t really have room. I thought, wouldn’t it be nice if there was something with a modular approach where when I need more, I can just add another one and another one.
“It’s not a completely unique idea - there are other things out there but they use basic MDF so more like what you might have in a club or bar setting, where it’s a bit more utilitarian and not as homely. Or there were other products that were crazy expensive… so I wondered how much they’d cost to make.
“I knew about Duke Makes because I’m a resident at their sister company and workspace, Duke Studios. The team put me in touch with Duke Makes, where I met Liam, told him what I was planning. He thought it was a good idea and it all went from there really.”
As with all our projects, when Chris came in we discussed his initial ideas and budget, the elements of the design that were most important to him, and the subtle touches that make products like this unique. We offered him an estimate and then got to work designing.
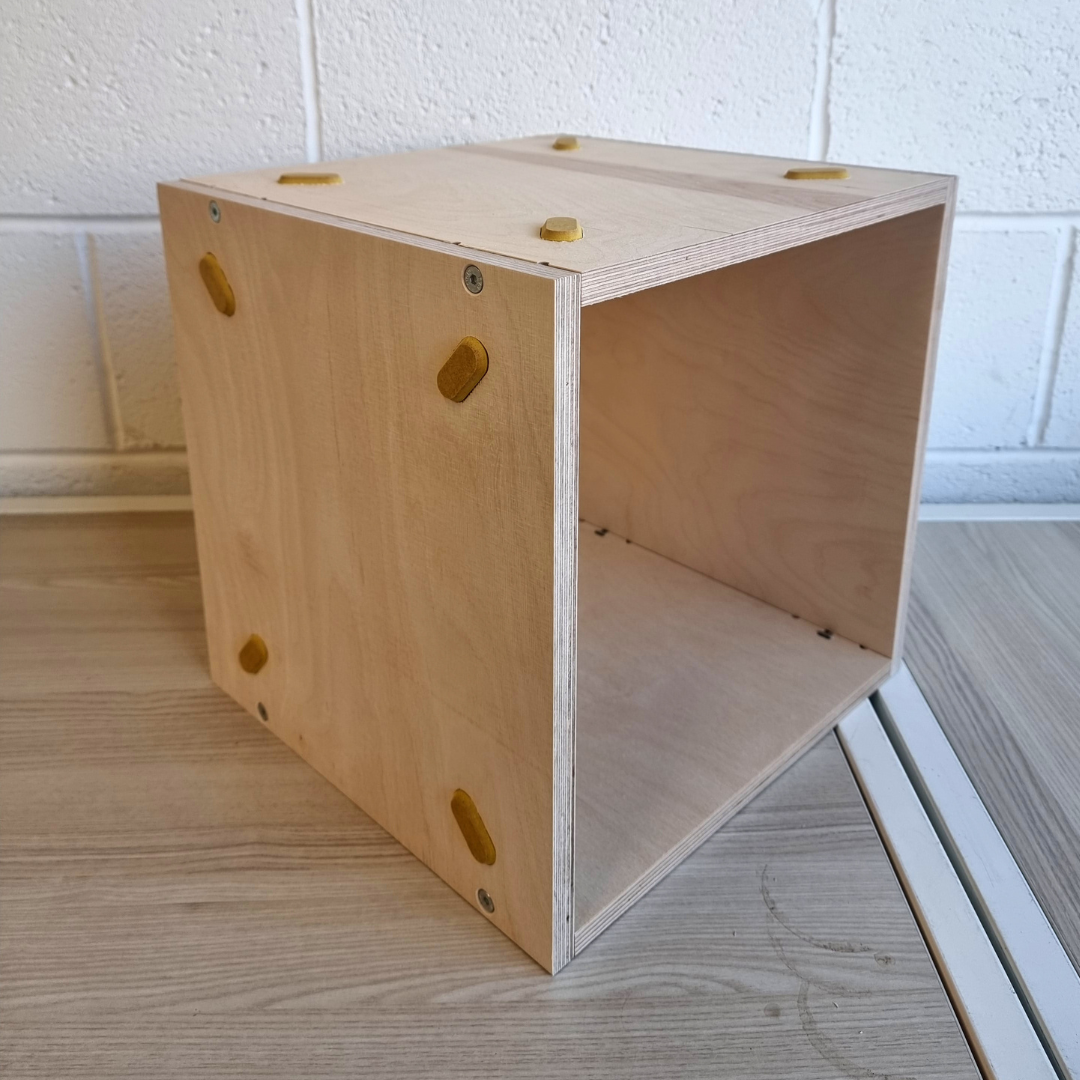
The Consultation and Design
“I had the idea but I didn’t have the design skills or software to do it. Liam was amazing. He really ran with with my concept and came up with this brilliant idea of how the units could lock together in a way that is very adaptable.
“One of the things that struck me with some of the other products that I had seen was the stackable wooden boxes. Vinyl is heavy, so I did know that once they were loaded they would probably stay quite still, but as someone with young children I wanted something a bit more secure and safe.
“The other thing I’d said was that I really like the idea of being able to have them stacked facing outwards but also have them flipped up like browse boxes on the top. Liam then took that and created a render with all of those elements!”
The 3D model is key because it visualises the outcome for the client, but also allows us to try different ideas out without the expense of manufacturing them. The system for securing each module was vital to Chris’s concept, so we used 3D modelling to find the perfect solution before we even touched the materials.
One of Chris’s main concerns was keeping costs low, so we created a design optimised for the Run CNC, making it quick to manufacture.
“He had some other ideas too - you could put a bench seat on top, some other adaptable bits and pieces. He really did move it into a different space away from purely just storage - this becomes a system of furniture, where you could put speakers or a turntable on top. Right now these things are to be developed down the line, but having these ideas from the start means that there’s room for add ons and edits.”
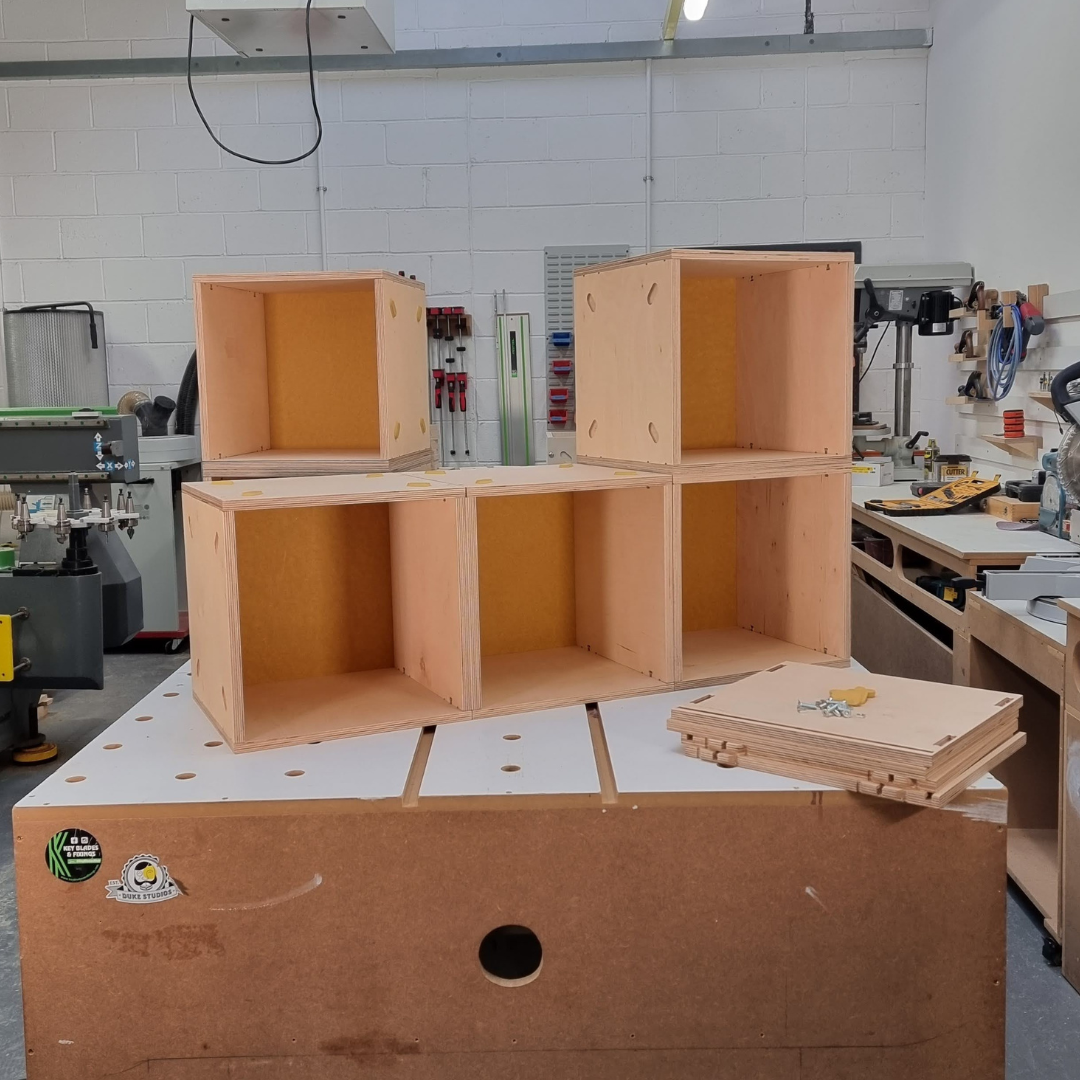
Prototyping
“I got them set up at home and then thought that it might be better if they were taller for records in a protective outer sleeve. Quite a few people wanted to know the dimensions because they looked tight, would they fit the sleeves in? So I spoke to Liam and asked if we had enough tolerance to get another 5mm height out of each one. Thankfully, he said yes!
“I really liked the way Liam had thought about the wood, the use of valchromat on the back of the units that’s a different colour to give it a bit of contrast. In the initial prototypes, the wood had a wax oil with a satin finish. That was very time consuming for Duke Makes to coat each piece, so Liam suggested getting the plywood in precoated in melamine that’s already finished, so it takes away that need to finish it. Being able to tweak things and get it right is the whole points of doing these prototypes.”
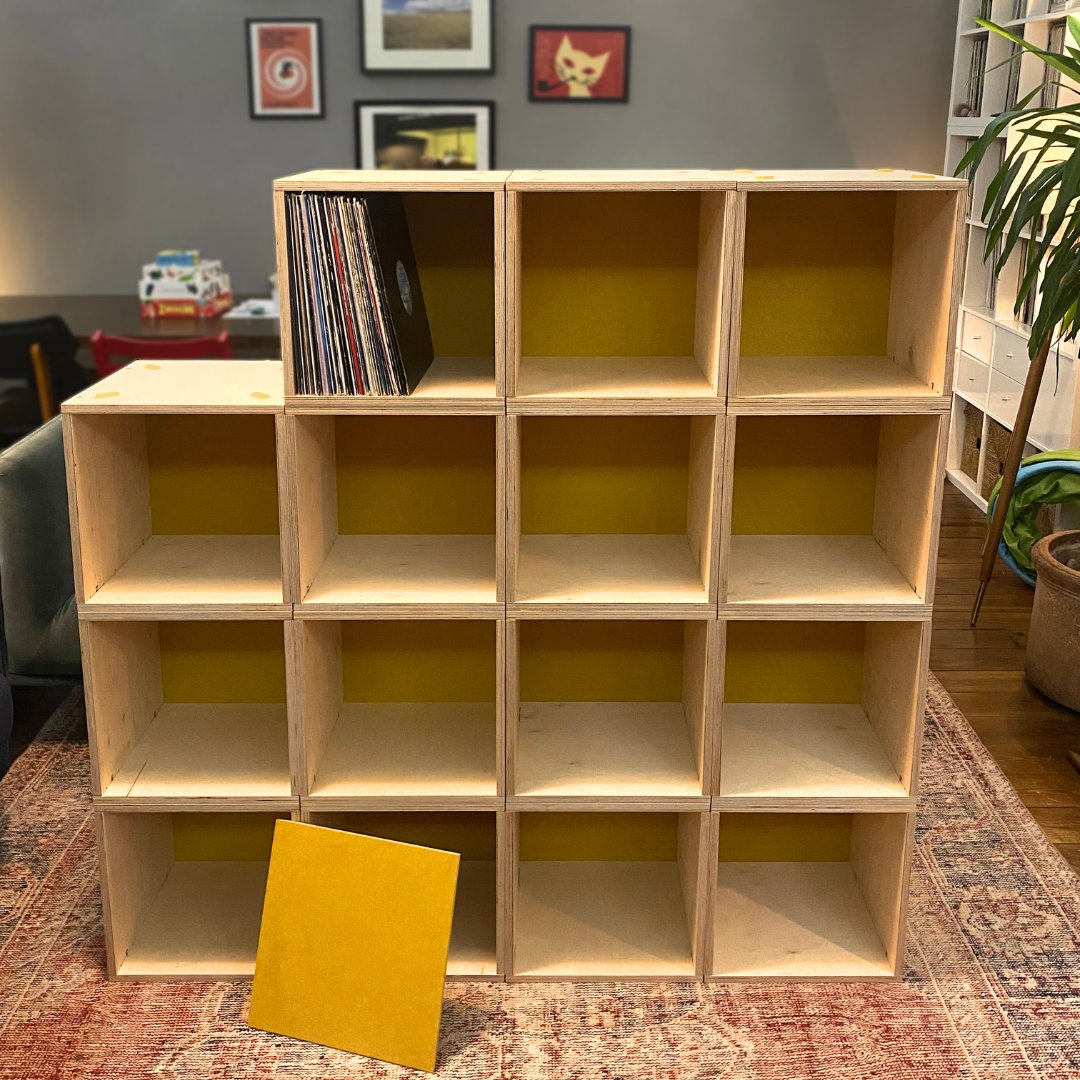
The Logistics
“The other thing that Liam and I talked about a lot was how they were going to be assembled and delivered. Would we create assembled units which were glued and pinned together? Or would it be flat pack, what are the pros and cons? We decided that the flatpack approach was the way to go because it makes it easier to ship them and is more economical. Going forward that also gave us more colour options for the valchromat backs.
“They’re four screws that go in that easily. It takes a few minutes to put together so it’s not complicated at all.”
The flatpack, modular design was intentional. By simply swapping the standardised Valchromat making up the ‘back’ panel, it allowed Chris the option of offering a range of colours without having to customise every single unit.
Our white-label design and create service is perfect for anyone who wants a unique product but doesn't want to deal with the hassle of designing and manufacturing it themselves. We take care of all the details, so that you can focus on what you do best - selling your product!
So, if you have a problem that needs solving or an idea that needs bringing to life, get in touch with us at Duke Makes. We're always happy to chat and help you find the perfect solution.
What to read next
about it
Get the latest news
Sign up to our newsletter to be the first to hear about everything we’re up to, and get early access to events, workshops and more.